- Veröffentlicht am 12. Jan. 2024
- Zuletzt bearbeitet am 12. Jan. 2024
- 8 min
Fehlermanagement
Fehlermanagement bezieht sich sowohl auf eine Unternehmenskultur, in der akzeptiert wird, dass Menschen Fehler machen und Prozesse kontinuierlich verbessert werden können, als auch auf Unternehmenspraktiken, die darauf abzielen, Probleme, die an Arbeitsplatz und Produktion auftreten, zu identifizieren, zu analysieren und zu beheben. In diesem Artikel werden die Bedeutung zur Vermeidung von Fehlern im Hinblick auf die Verbesserung der Produktivität und der Kundenzufriedenheit erläutert.

Ein ganzheitliches Fehlermanagement umfasst sowohl die Betrachtung von Anfälligkeiten und Risiken in der Mensch-Maschinen-Interaktion, als auch das mögliche Auftreten von ungeplantem, technischem Versagen. Ziel eines jeden Fehlermanagements sollte es sein, Abweichungen in Produktion oder Betrieb so frühzeitig wie möglich zu identifizieren, um rechtzeitig Gegenmaßnahmen entwickeln und einleiten zu können. Daher beinhaltet jede Phase dieses Prozesses Maßnahmen und Werkzeuge zur
- Fehlerentdeckung/-identifikation
- Fehlerdiagnose/-analyse
- Fehlerkompensation (Sofortmaßnahmen sowie mittel- und langfristige Lösungen)
- Fehlerkorrektur
Fehler können sowohl im technischen Betrieb, Produktionsprozessen sowie Wartung und Instandsetzung auftreten, als auch in administrativen und Management-Abläufen. Eine wichtige Voraussetzung für den professionellen und nachhaltigen Umgang mit Abweichungen ist eine klare Festlegung von Zielen, Standards und Qualitätsanforderungen, die vorrangig auch auf die Sicherheit aller Mitarbeitenden abzielen muss. All diese Anforderungen müssen messbar sein, regelmäßig überwacht werden und bedürfen einer offenen Fehlerkultur, die auf einem kontinuierlichen Verbesserungsprozess (KVP) beruht.
Operational Excellence
Die Operational Excellence (oder operative Exzellenz) beschreibt die ständige, ganzheitliche und kontinuierliche Betrachtung aller Unternehmensprozesse in Bezug auf ihre Wirtschaftlichkeit und Qualität. Erste Mittel hierfür sind die Definition und Messbarmachung der vorhandenen Prozesse, denn nur so können Abweichungen erfasst und Optimierungspotenziale identifiziert werden.
Die Operational Excellence bedient sich vorrangig Methoden des Lean Management, das heißt einer integrierten, auf Wertschöpfung ausgerichtete Prozessoptimierung, die alle Arten von Verschwendung vermeidet. Ein Ziel dabei ist, nicht nur Fehler zu identifizieren und analysieren, sondern Prozesse so zu gestalten, dass Fehler von vornherein gar nicht erst entstehen können.
Lean Management
Als Teilbereich des Lean Managements spielt vor allem die schlanke Produktion (“Lean Production”) eine entscheidende Rolle beim Fehlermanagement. Nur durch Messbarmachung des Herstellungsprozesses können Fehler frühzeitig erkannt werden und somit dem Null-Fehler-Prinzip der Lean Production gerecht werden. Je früher ein Fehler erkannt wird, desto weniger Folgekosten entstehen. Mit dieser Methode soll vermieden werden, dass sich Fehler in die folgenden Arbeitsschritte verschleppen und zu kostenintensiver Nacharbeit oder gar Neuproduktion oder Rückrufaktionen führen.
Daher ist neben einer kontinuierlichen Prozessüberwachung auch eine Analyse und Dokumentation der aufgetretenen Fehler wichtig, wobei auch der Prozess selber, wie mit aufgetretenen Fehlern zu verfahren ist, festgehalten sein sollte.
Zu erwähnen ist neben der schlanken Produktion auch der Einfluss einer schlanken und professionell geplanten Instandhaltung zur Vermeidung von Prozessfehlern.
KVP
Der kontinuierliche Verbesserungsprozess (KVP, auch CIP- Continuous Improvement Process genannt) ist eine Strategie des Qualitätsmanagements, dessen Ziel es ist, die Produktionsprozesse ständig in kleinen Schritten hinsichtlich ihrer Wertschöpfung, Effizienz aber auch Sicherheit und Messbarkeit zu verbessern.
Hauptgedanke hierbei ist ein schrittweises, integriertes Vorgehen, das weder eines aufwändigen Stillstandes noch größerer Umbaumaßnahmen bedarf. Verbesserungspotenzial kann jederzeit und von jedem Mitarbeiter, der an dem Prozess beteiligt ist, identifiziert werden. In diesem Sinne sollten Führungskräfte ihre Mitarbeiter motivieren, eigene Ideen zur Produkt- und/oder Prozessverbesserung zu kommunizieren.
Eine aufgeschlossene Fehlerkultur im Unternehmen ist eine wichtige Voraussetzung, um Prozesse sicher und effizient zu gestalten.
Zudem ist es sinnvoll, ein Bewusstsein für die Auswirkung von Fehlern auf nachfolgende Bereiche, Sicherheit und Umwelt zu schaffen. Umgesetzte Verbesserungsmaßnahmen sollten stets auf ihre Wirksamkeit hin überprüft werden, zudem ändern sich häufig Randbedingungen, sodass Produktionsprozesse regelmäßig revidiert werden sollten (PCDA Zyklus: Plan-Do-Act-Check).
Lessons Learned
Die ursprünglich aus dem Projektmanagement stammende Lessons-Learned Strategie, bei der Erkenntnisse aus abgeschlossenen Projekten in die Planung zukünftiger Projekte mit einfließen sollen, bewährt sich ebenfalls für die Ergebnisse aus Fehleranalysen in der Produktion.
Entscheidend ist eine Dokumentation der Erkenntnisse und welche kurz-, mittel- und langfristigen Maßnahmen beim Beheben des Fehlers erfolgreich waren bzw. zur zukünftigen Vermeidung führen. Diese Maßnahmen müssen allen Prozessbeteiligten zur Verfügung stehen. Im Rahmen eines ganzheitlichen Wissensmanagement ist es oft sinnvoll, ein organisationsinternes System zur Verwaltung dieser Dokumentation zu etablieren.
Im Lessons Learned bzw. Qualitätsmanagement wird häufig zwischen korrektiven Maßnahmen und präventiven Maßnahmen unterschieden (CAPA- corrective action / preventive action).
Trotz des Fokus des Lessons Learned auf Verbesserungspotenzial und Fehlervermeidung sollten in diesem Rahmen durchaus auch positive Erkenntnisse benannt und identifiziert werden, damit auch diese, im Sinne einer Best-Practice-Philosophie, in den neuen Prozess mit einfließen können.
Qualitätsmanagement
Ein professionelles Fehlermanagement braucht ein funktionales und strukturiertes Qualitätsmanagement. Im Qualitätsmanagement werden die Grundlagen für sichere und messbare Arbeitsabläufe geschaffen, die eine stabile Produktion mit möglichst geringen Fehler- und Ausfallzeiten gewährleisten sollen. Wichtigste Maßnahmen sind das Festlegen von Toleranzen, Frequenz und Art der Prozessüberwachung sowie das Sicherstellen eines kontinuierlichen Verbesserungsprozesses.
Durch regelmäßige Audits werden Prozesse auf die Einhaltung dieser Vorgaben hin untersucht.
Alle Methoden des Qualitätsmanagements bedürfen einer aktuellen Dokumentation, um zu gewährleisten, dass die bestehenden Abläufe noch zu den sich häufig ändernden Randbedingungen passen, und dass die Erkenntnisse aus Fehleranalysen auch in die entsprechenden Fachbereiche zur Prävention gelangen.
Das Qualitätsmanagement spielt eine zentrale Rolle bei der Fehlerprävention und -analyse und sollte bei allen Entscheidungen mit einbezogen werden.
Fehlermanagement bezieht seine Methoden aus einem professionellen Qualitätsmanagement.
Zehnerregel der Fehlerkosten
Wie bereits erwähnt, ist der Zeitpunkt der Entdeckung der Abweichung von entscheidender wirtschaftlicher Wichtigkeit. Nachdem durch Vorgaben des Qualitätsmanagements zunächst einmal definiert wurde, wie ein Fehler definiert ist (z. B. das Vorliegen von Messergebnissen außerhalb einer bestimmten Toleranz) wird der Prozess in regelmäßigen Abständen oder sogar permanent überwacht und ein Soll-/Ist-Vergleich vorab festgelegter Prozesskenngrößen gefahren. In diesem Rahmen muss die gesamte Wertschöpfungskette betrachtet werden, denn ein Fehler wird umso teurer, je später er entdeckt wird.
Die sogenannte "Zehnerregel der Fehlerkosten” aus dem KVP besagt, dass sich die Kosten der Fehlerbehebung mit jedem Prozessschritt, in dem der Fehler entdeckt wird, verzehnfachen wobei gleichzeitig die Möglichkeit Abstellmaßnahmen einzuleiten, im gleichen Faktor abnimmt.
Eine offene Fehlerkultur ist also unerlässlich und sollte sowohl zum Wohle des Produktes als auch der Mitarbeitenden von den Unternehmensverantwortlichen vorgelebt werden.
Einsparpotenzial
Aus der Zehnerregel der Fehlerkosten lässt sich ableiten, dass ein frühzeitiges Erkennen von Prozessabweichungen sowohl die Möglichkeiten der Einflussnahme erhöht, als auch enormes Einsparpotential bietet.
Verschiedene Werkzeuge der Fehleranalyse bieten die Möglichkeit, nicht nur Ursachenforschung zu betreiben, sondern Fehler auch nach ihrer Häufigkeit, Komplexität und Auswirkung hin zu kategorisieren.
Das Ishikawa-Diagramm (oder Fischgräten Diagramm, benannt nach dem japanischen Wissenschaftler Kaoru Ishikawa) u. a. bietet beispielsweise eine Übersicht aller Faktoren, die Einfluss auf die Qualität eines Prozesses haben:
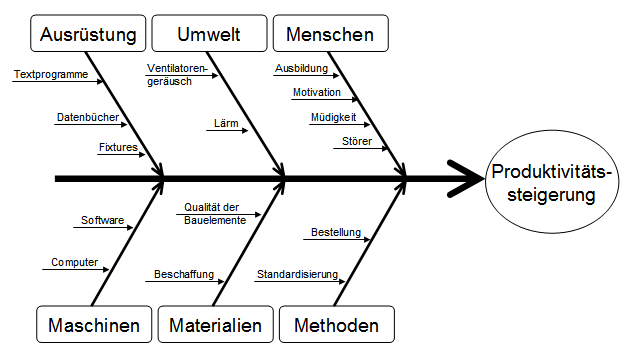
An dieser Übersicht ist gut zu erkennen, welche Ressourcen Einfluss auf die Produktqualität haben und damit Fehlerpotenzial bieten.
Offenheit
Eine offene Fehlerkultur sollte alle Mitarbeitenden motivieren, selbst verursachte Missstände vertrauensvoll und rechtzeitig zu kommunizieren, ohne Einbußen bezüglich der Karriere fürchten zu müssen. Führungskräfte sollten ihr Team bezüglich der Auswirkungen von verdeckt gehaltenen Fehlern sensibilisieren und immer wieder aufzeigen, wie groß die Einflussnahme am gesamten Prozess ist, werden Fehler rechtzeitig erkannt und gemeldet.
Diese Art der Offenheit erfordert auch ein positives Vorleben von Fehlermanagement von Mitarbeitenden in Führungspositionen. Ziel einer gesunden Organisation sollte es stets sein, schnell und effizient auf Missstände reagieren zu können und Abhilfemaßnahmen als Teamleistung zu erarbeiten - sowohl in der Fehlerkorrektur als auch in der Vermeidung.
Auch ein betriebliches Vorschlagswesen kann dazu beitragen, potenzielle Fehlerquellen zu identifizieren und die Produktionsprozesse sicherer und effizienter zu gestalten.
Mensch-Maschine Schnittstelle
Ist ein Prozess fast oder vollständig automatisiert, birgt die Möglichkeit oder das Erfordern des manuellen Eingreifens durch eine Mensch-Maschine-Schnittstelle dennoch Fehlerpotenzial. Um diese Risiken zu minimieren, wird häufig das Poka-Yoke-Prinzip angewendet, dessen Ziel es ist, potenzielle Fehler möglichst frühzeitig im Prozess gar nicht erst entstehen zu lassen. Das heißt, dass ein Prozess oder eine Apparatur derart gestaltet ist, dass eine Bedienung oder Bestückung konstruktiv nur auf eine bestimmte Art möglich ist und Fehlanwendungen damit ausgeschlossen werden können. Ein klassisches Beispiel ist das Entnehmen von Bargeld auf dem Geldautomaten, das erst möglich ist, nachdem die Geldkarte dem Benutzer wieder ausgehändigt wurde. Das Vergessen der Karte ist damit unmöglich geworden. Auch lassen sich viele Stecker oder Anschlüsse nur auf eine bestimmte Art installieren, so dass auch eine Fehlanwendung durch den Benutzer ausgeschlossen werden kann.
Die Schnittstelle zwischen Mensch und Prozess bzw. Maschine sollte also gründlich auf potenzielle Fehlerquellen hin untersucht werden und so anwenderfreundlich und sicher wie möglich gestaltet werden.
Fehleranalyse
Zur Fehleranalyse haben sich verschiedene Methoden bewährt. Zu den bekanntesten Vorgehensweisen gehören:
Die klassische RCA (Root Cause Analysis) untersucht Fehler hinsichtlich einer oder mehrerer Entstehungsgründe, klassifiziert diese nach Schwere, Häufigkeit und Folgekosten und definiert Abstellmaßnahmen. Diese können neben Prozessanpassungen auch Veränderungen in der Methodik sein.
Der 8-Report dient der Qualitätssicherung nach einer (internen oder externen) Reklamation und muss zeitnah nach Bekanntwerden des Fehlers initiiert werden. Er beinhaltet weitestgehend die aus dem Six-Sigma bekannten Prozessschritte DMAIC (Define – Measure – Analyse – Improve – Control, also Definieren – Messen – Analysieren – Verbessern – Steuern).
Die 5-Why Methode fragt bei einem aufgetretenen Problem 5-mal nach dem "Warum", um an den ursächlichen Grund zu gelangen.
Die FMEA (Fehler-Möglichkeiten Einfluss Analyse) benutzt Kennzahlen, um potenzielle Fehler oder qualitative Abweichungen dahingehend zu bewerten, wie wahrscheinlich ihr Auftreten, ihre Entdeckung und welche Auswirkungen sie haben können.
Ziel dieser Methode ist es, Fehlerrisiken von vornherein zu identifizieren, zu minimieren oder zu vermeiden.
Einem erfolgreichen Fehlermanagementprozess liegt die Bereitschaft eines Unternehmens zugrunde, Fehler einzugestehen, auszutauschen und daraus zu lernen. Spezifische Praktiken und Instrumente können maßgeschneidert eingesetzt werden, um den gesamten Produktlebenszyklus zu verbessern. Zusätzlich können gezielte Schulungen ebenfalls in Betracht gezogen werden, um den Prozess zu optimieren.
Langfristig wird ein erfolgreiches Fehlermanagement nicht nur die Produktivität steigern, sondern auch die Kosten senken, zur Innovation beitragen und die Kundenzufriedenheit erhöhen. Lassen Sie sich in diesem Artikel inspirieren, wie Sie Ihren eigenen Fehlermanagementprozessstrukturieren können, und stöbern Sie in unserem Shop nach den Werkzeugen und Geräten, mit denen Sie die Produktivität Ihrer Anlage verbessern können.