- Veröffentlicht am 6. Sept. 2024
- Zuletzt bearbeitet am 6. Sept. 2024
- 7 min
Was ist Pneumatik?
Dieser Leitfaden soll die Grundprinzipien der Pneumatik erläutern. Es werden die verwendeten Werkzeuge und zugehörigen Komponenten dieser Technologie, konstruktive Grundlagen sowie die Einsatzgebiete der Pneumatik beschrieben.

Die Pneumatik basiert auf der Nutzung von komprimierter Luft, die zur Verrichtung von Arbeit technisch aufbereitet und gesteuert wird. Die Bezeichnung Pneumatik geht auf das griechische Wort Pneumos - im Sinne von Hauch, Windhauch - zurück. Erste Anwendungen finden sich bereits in Form von einfachen Blasebälgen in der Antike, die zum Anfachen von Feuern im Rahmen früher Metallverarbeitung genutzt wurden.
Zu Beginn des 20. Jahrhunderts verbesserte der Einsatz von Ventilen die industrielle Produktion, indem Druckluft durch gezielte Steuerung für Kraftübertragungen in Arbeitsabläufen eingesetzt wurde. Maschinen und Anlagen wurden somit genauer und effizienter.
Heute ermöglichen pneumatische Luftfederungen Fahrkomfort in Autos und landwirtschaftlichen Fahrzeugen, aber auch in modernen Technologien wie Robotik und Prozessautomatisierung führt sie zu präzisen und störungsfreien Bewegungen, die sich auch die Forschung und Entwicklung zunutze macht.
Die Grundlagen der Pneumatik
Ein pneumatisches System setzt sich im Allgemeinen aus 4 Komponenten zusammen:
- die Drucklufterzeugung
- die Druckluftaufbereitung
- die Druckluftverteilung und -steuerung sowie dem
- Anwendungssystem
Anwendungen können unterschiedlichster Art sein und daher verschiedene Drücke erfordern. Kompressoren erzeugen daher Drücke von 6 bis zu 40 bar. In pneumatischen Anwendungssystemen wird dagegen häufig der Luftverbrauch pro Zeiteinheit oder Arbeitsgang als Vergleichsgröße angegeben. Die Einheit ist Normkubikmeter oder Normliter, bezogen auf den als physikalischen Normzustand definierten Standarddruck von pn= 1,01325 bar und die Standardtemperatur von Tn=0o Celsius bzw. 273,15 Kelvin.
Die Vorteile der Pneumatik - besonders im Vergleich zur Hydraulik - liegen in der vergleichsweise einfachen Wartbarkeit der einzelnen Komponenten, dem umweltfreundlichen Medium (Luft) und der schnellen Reaktionsfähigkeit, die diese Technologie für serielle Fertigungen und Automatisierungstechnik besonders attraktiv macht.
Drucklufterzeugung
Für die pneumatische Nutzung wird das Medium Luft mittels eines Kompressors verdichtet.
Im Allgemeinen werden - je nach Bauart, Funktionsweise und Anwendungsgebiet die folgenden Verdichtertypen unterschieden:
- Kolbenverdichter: der Arbeitsraum befindet sich zwischen Kolben und Zylinder (Pneumatik Zylinder), hier wird die mit Unterdruck angesaugte Luft verdichtet und anschließend weitergeleitet. Die Bewegung des Kolbens (meist mehrere) wird durch einen Elektromotor, gelegentlich auch einen Verbrennungsmotor erzeugt
- Schraubenverdichter: im Grunde eine Variante des Kolbenverdichters, da auch hier die Drehkolben eine Rotationsbewegung ausführen und die Komprimierung der Luft zwischen Kolben und Gehäuse stattfindet. Das Besondere ist hier der zweiwellige Betrieb, bei dem die Wellen spindelförmig ineinander greifen
- Turboverdichter: zumeist mehrstufiger Kompressor, charakteristisch ist ein Läufer mit umgebendem Kompressionsgehäuse, in dem das Gas verdichtet oder - ja nach Bauart- entspannt wird. Leit- und Laufschaufeln lenken den Luftstrom und führen zu den gewünschten Druckveränderungen des Gases.
Allen Verdichtertypen ist gemein, dass sie das Volumen des Mediums (hier: der Luft) verringern, was gleichzeitig eine Erhöhung des ursprünglichen Druckes, aber auch der Ausgangstemperatur zur Folge hat. Bleibt die dabei entstehende Wärme ungenutzt, liegt eine geringe Energieeffizienz des Systems vor.
[H3] Druckluftaufbereitung
Damit die komprimierte Luft im Verteilungssystem oder während der Anwendung keine Schäden an den Komponenten verursacht, muss sie von Fremdkörpern (Staub, Kleinteile, Späne usw.) gereinigt und möglicherweise auch getrocknet werden. Mit Letzterem wird Korrosion an den Bauteilen vermieden.
Die Aufbereitung der Druckluft mit Filtern und Trocknern kann unmittelbar nach der Kompression an der Kompressorstation erfolgen oder, abhängig von Größe und Anwendungsfall, in einer externen Station. Je nach Volumen und Qualitätsanforderung an die Druckluft kann es notwendig sein, Filter häufig zu warten oder auszuwechseln. Eine dezentrale Aufbereitung als Teil der Wartungseinheit Pneumatik kann die Instandhaltung erleichtern aufgrund einer einfacheren Zugänglichkeit.
Filter und Trocknungsaggregate stellen einerseits die notwendige Qualität sicher, andererseits bringen sie auch Druckverluste mit sich, die nur durch regelmäßiges Warten und Auswechseln gering gehalten werden können.
Druckluftverteilung und Steuerung
Ist die Luft komprimiert und möglichst verlustarm aufbereitet, wird sie -teilweise durch komplexe Rohrleitungssysteme- an die Verbrauchsstellen geleitet. Dabei stellen Pneumatik-Steckverbinder wesentliche Komponenten in pneumatischen Systemen dar, da sie eine einfache und sichere Verbindung von Schläuchen und Leitungen ermöglichen. Den Rohrdurchmesser und -topologien kommt dabei eine besondere Rolle zu, da sie Einfluss auf die Strömungsgeschwindigkeit haben. Zudem müssen Leckagen überwacht und schnell behoben werden, um Energieverluste zu minimieren.
Pneumatikventile bzw. Stellglieder steuern den Einsatz der Druckluft. Sie spielen in der Pneumatik eine zentrale Rolle, da sie den Durchfluss von Druckluft steuern und somit die Bewegung und Funktion von pneumatischen Systemen regeln.
Zu den klassischen Ventilarten gehören:
- Wegeventile
- Rückschlagventile
- Druckregelventile
- Stromregelventile
- Schnellüftungsventile
- Logikventile
Jede Ventilart hat ihre spezifischen Anwendungsbereiche und ist für unterschiedliche Anforderungen in pneumatischen Systemen konzipiert.
Neuigkeiten aus unseren 5 passenden Branchenlösungen
Entdecken Sie spannende Neuigkeiten aus den Bereichen Design, Maschinenbau, Instandhaltung, Beschaffung sowie Sicherheit & Schutz
Betätigungsarten der Pneumatik
Abhängig von den Anforderungen des Anwendungsbereichs gibt es unterschiedliche Möglichkeiten, ein pneumatisches System zu betätigen. Dabei spielen Geschwindigkeit, die benötigte Kraft, Präzision und auch Sicherheitsaspekte eine entscheidende Rolle.
Viele Einrichtungen können oder müssen manuell betätigt werden, wenn es um einfache Anwendungen wie beispielsweise ein 3/2-Wegeventil zur Steuerung eines einfachwirkenden Zylinders geht.
Dagegen werden bei der elektrischen Betätigung elektrische Signale (Elektro-Pneumatik) genutzt, um pneumatische Komponenten zu steuern. Dies geschieht durch Magnetventile, die durch elektrischen Strom aktiviert werden. Diese Art der Betätigung ermöglicht eine präzise und schnelle Steuerung. Dies ist bei SPS Steuerungen der Fall und in seriellen Fertigungsprozessen.
Ist eine elektrische Ansteuerung nicht mehr möglich oder sicher, kann das pneumatische System selbst durch eine pneumatische Vorrichtung betätigt werden. Die Bewegung eines Zylinders oder ein Ventil wird dabei per Druckluft ausgelöst.
Seltener findet man auch hydraulische Ansteuerungen in pneumatischen Vorrichtungen. In solchen Fällen wird ein hydraulischer Druck genutzt, um einen pneumatischen Aktor zu steuern. Dies kann hilfreich sein, wenn hohe Kräfte bei kleinerem Volumen erforderlich sind.
Instrumente und Werkzeuge
Die Komponenten eines pneumatischen Systems finden sich in einem Pneumatik Schaltplan wieder. Pneumatik Symbole und Pneumatik Schaltzeichen sind standardisiert und vereinfachen damit die Orientierung in teilweise komplexen Topologien.
Grundlegende Schaltzeichen und Bestandteile eines pneumatischen Schaltplans sind:
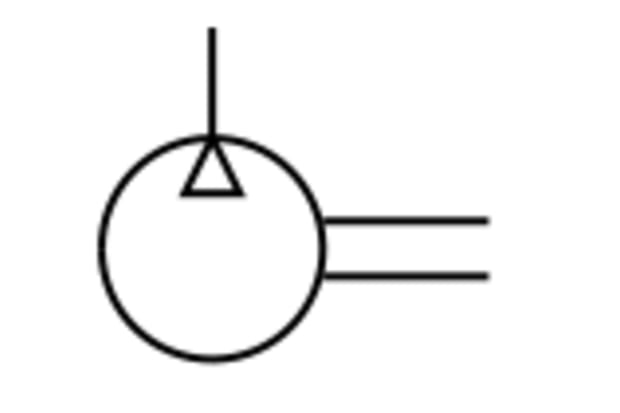
der Kompressor bzw. Verdichter
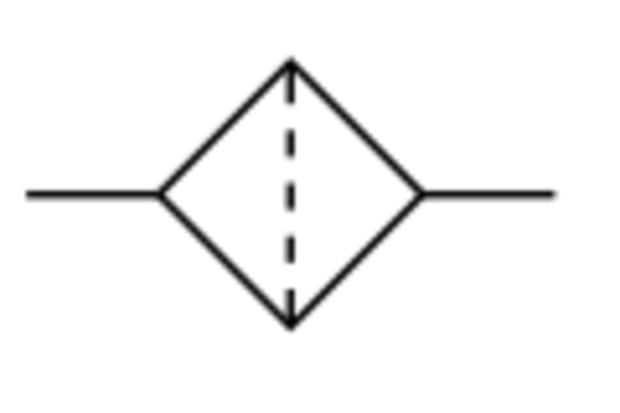
ein einfacher Filter
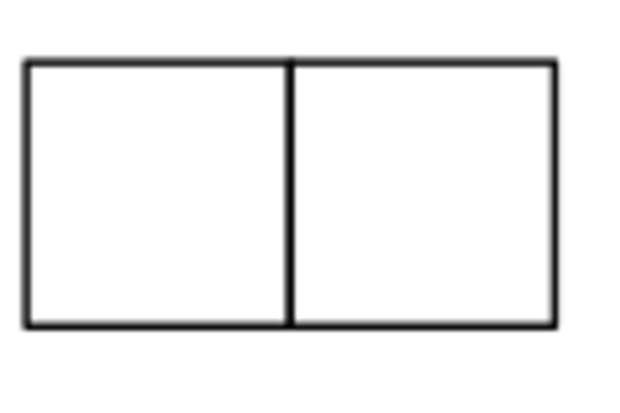
ein Wegeventil (hier mit 2 Schaltstellungen)
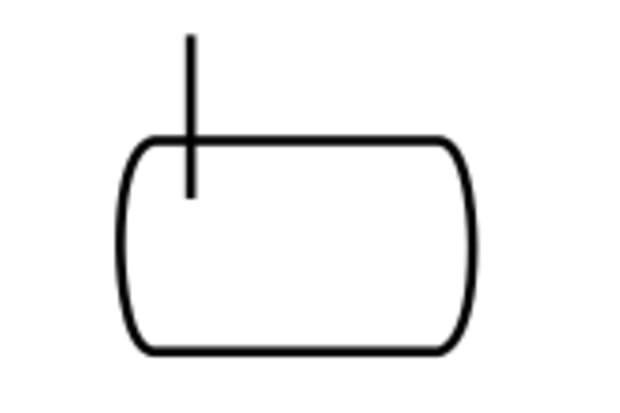
ein Druckluftspeicher
Daneben existieren eine Vielzahl von Symbolen u.a. zur Temperatur- und Druckregelung, über die die einschlägige Literatur informiert.
Zur Wartung und Instandhaltung kommen unterschiedliche Mess- und Prüfgeräte zum Einsatz. Um hier einen reibungslosen Service gewährleisten zu können, ist es entscheidend, die Instrumente der Pneumatik Wartungseinheit selbst regelmäßig zu überprüfen und ggf. zu kalibrieren.
Zu diesen Instrumenten zählen Druck- und Durchflussmesser sowie elektronische oder mechanische Lecksuchgeräte. RS bietet neben den erforderlichen Messgeräten auch den zugehörigen Kalibrierservice an.
Der Einsatz von Pneumatik in der Industrie
Da pneumatische Anwendungen eine Reihe von Vorteilen bieten, wie eine einfache Steuerung, schnelle Bewegung ermöglichen und einen hohen Grad an Sicherheit und Zuverlässigkeit ermöglichen, sind sie in der Industrie weit verbreitet.
Ihr Einsatz erstreckt sich von einfachen Sprüh- und Reinigungssystemen über industrielle Serienfertigung und Automatisierungstechnik bis hin zu hochpräzisen Anwendungsfällen zur Positionierung in Medizintechnik oder der Nanotechnologie.
Eine regelmäßige Wartung ist die Voraussetzung für einen sicheren Betrieb der Pneumatiksysteme, denn nur so können Verunreinigungen, Korrosion und letztendlich auch Druckverlust vermieden werden.
Pneumatik und ihre Auswirkung auf eine nachhaltige Industrie
Pneumatische Anwendungen spielen eine entscheidende Rolle bei der Weiterentwicklung nachhaltiger Technologie und Produktionsmethoden. Gezielt eingesetzt können moderne pneumatische Systeme sehr effizient betrieben werden, insbesondere wenn Druckverluste minimiert und Komponenten richtig dimensioniert sind.
Auch die Drucklufterzeugung selbst bietet viel Potential für ressourcenschonendes Wirtschaften, indem die bei der Komprimierung des Mediums entstehende Wärme für verschiedene Prozesse genutzt wird. Diese kann als Luft- oder Fußbodenheizung, aber auch als Prozesswärme eingesetzt werden. Ebenso kann die Abwärme zur Erwärmung von Wasser für sanitäre Einrichtungen, Küchen oder Produktionsprozesse verwendet werden.
Die Nutzung der Abwärme bietet den Vorteil der Energieeinsparung, Kosteneffizienz und trägt zur CO2-Reduzierung bei.
Druckluftsysteme erzeugen keine direkten Emissionen während des Betriebs und stellen somit eine saubere Energiequelle dar. Bei der Verwendung von erneuerbaren Energien zur Erzeugung der Druckluft kann der CO2-Fußabdruck ebenfalls weiter reduziert werden.
Zudem sind pneumatische Systeme oft langlebig und zuverlässig, was zu einer längeren Lebensdauer der Maschinen und geringeren Wartungskosten führt. Eine regelmäßige Wartung ist dennoch unerlässlich.